
hydroform
process
A leader since 1923, F&B Manufacturing experience in hydroforming brings cost effective solutions in sheet metal to it’s customers. An expert staff brings knowledge to the fabrication process and sees projects all the way to completion.
Our hydroform process produces unique results that meet or exceed customer specifications. The four step process involves the following:
Positioning
Forming chamber is raised, and then blank is placed on draw ring.
Initial Pressure
Forming chamber is lowered and pressure is applied.
Variable Pressure
Variable controlled pressure allows blank to conform as punch moves upward.
Pressure Release
When pressure is released, forming chamber rises with punch position lowered away from finished part.
HYDROFORMING
IN ACTION
Hydroforming involves the application of pressurized hydraulic fluid to form metal into shapes that would be challenging to achieve with other techniques. Typical fabrication materials include high temperature alloys, steel, titanium, aluminum, copper and brass.
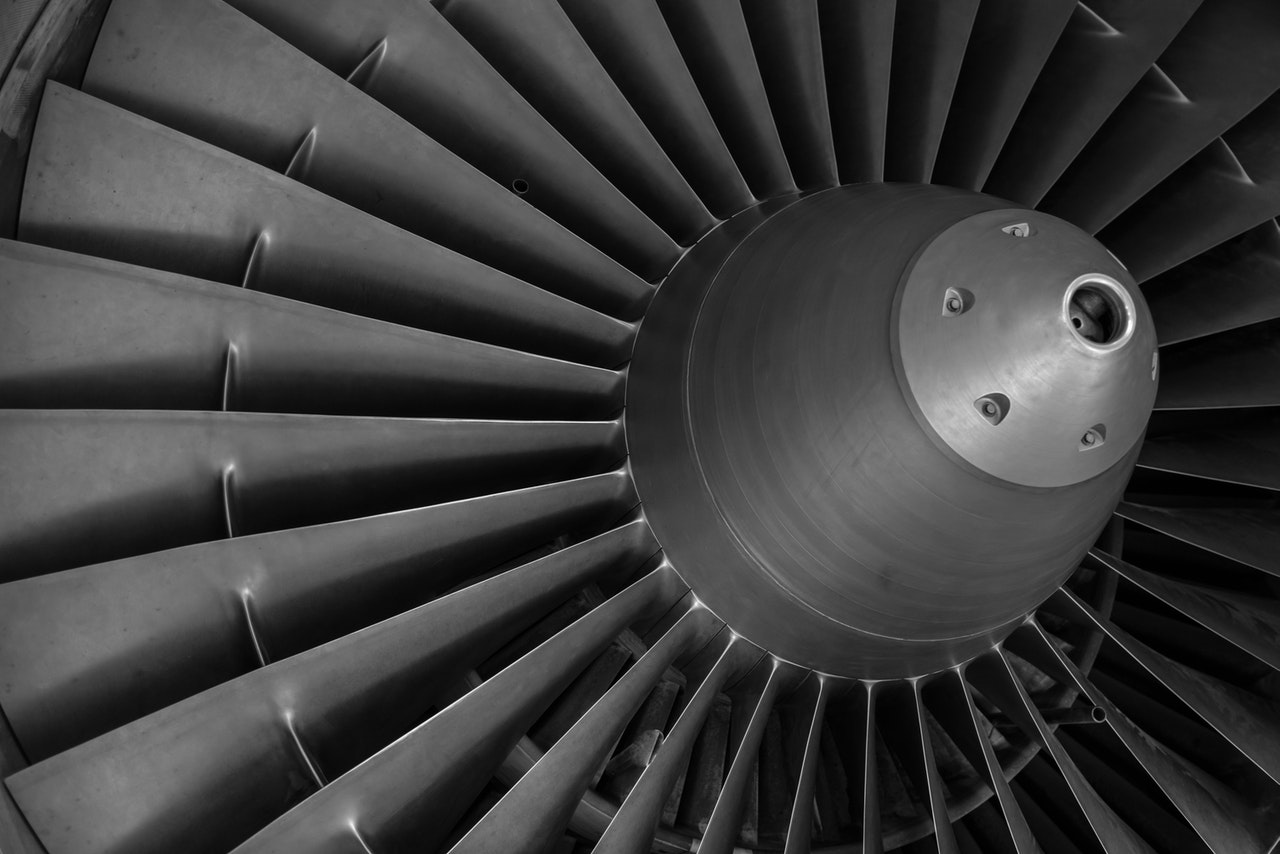
Play Video

OUR PROCESS
IS CERTIFIED
What will our unique AS9100 certified hydroform process process mean to you?
- Improves Metal Values – the process eliminates need to polish or finish parts. The exterior surface is smooth and uniform with minimal thin-out in the cross sectioning.
- Reduces Tooling Costs – Hydroforming does not require mating male and female dies that are needed in alternate processes. Often, a single punch is the only unique tool needed to hydroform metal”.
- Ideal for Production & Development – The F&B hydroforming process simplifies tooling modifications by accommodating a range of material thicknesses with the same tooling.
- Exceptional Tolerance Control – precise tolerance results from our hydroforming process.
- Reduced Processing Costs – Reduces the need to polish or blend surfaces imperfections. Resulting surfaces after hydroforming are uniform in appearance, usually requiring no mechanical finishing